In business and manufacturing applications, cables, hoses, and hydraulic lines need protection in the form of cable carriers or cable tracks. There are both light and heavy-duty choices with high-performance requirements. The application might need to protect against heat, debris, and abrasives. It is important for business owners to find a reliable source of high-quality cable and hose carriers to protect their equipment investment. There is also a choice between metal and plastic cable carriers
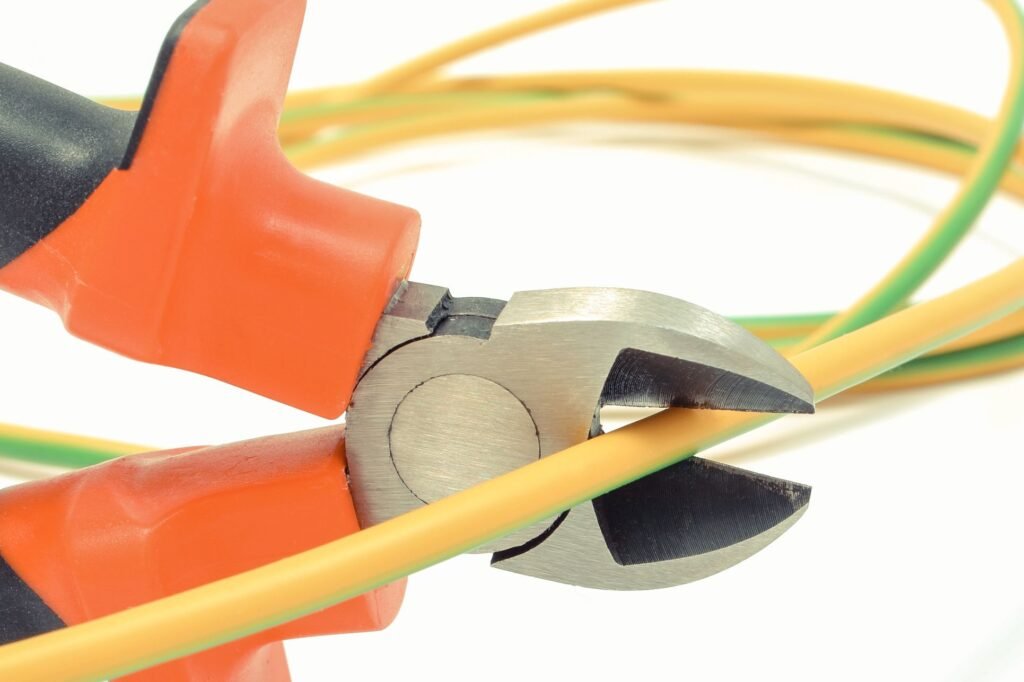
Cable and hose carriers are defined as flexible hollow constructions that are composed of multiple links to assist in guiding and protecting cables, hydraulic lines, and hoses on machinery and equipment in industrial settings. These carriers come in either plastic or metal.
The first metal steel carrier was introduced in the 1950s. Before that point, hoses and cables were left hanging from machines where they were often damaged and wore out quickly. The metal and, soon after, plastic carriers served the important purpose of protecting hoses and cables and allowing them to last much longer. They also prevented lines from getting tangled and improved worker safety.
Carriers can be designed and installed to accommodate lines that are traveling horizontally, vertically, rotary, and three-dimensionally. These carriers are most often rectangular in a cross-section and have crossbars located along their length to be opened from the outside to insert cables or inspect cables and hoses.
Contents
Plastic or Metal Carriers?
These considerations will inform your decision about which material to choose for carriers:
- Temperature makes a difference. Heavy loads and high operating temperatures call for steel carriers. The company representative can help with this determination.
- Speed might be a limiting condition for steel carriers. Plastic carriers such as nylon are a good choice where applications need higher speeds. But, when there are longer unsupported spans and heavier loads, metal might be the better choice. Some steel carriers are designed for greater speed applications.
- The link style can be either enclosed or accessible. Open style carriers make inspections easier, while enclosed carriers protect cables and hoses against shavings, sparks, and hot chips.
- The bend radii required will also affect the decision of going with nylon or steel. The minimum bend radius required is an important factor in selecting the correct carrier. Electrical cables can be rated for a radius of 7.5 times the outside diameter of the cable. Hoses may have a minimum radius bend of 12 times their outside diameters.
Plastic Cable and Hose Carriers
Plastic cable carriers molded with high-strength, glass-filled nylon or even special polymers are very durable and resist corrosion. Plastic carriers are good for installations that require high speed or acceleration. They are also good for applications requiring long travel operations.
Temperature makes a difference, and glass-filled plastic carriers have an operating temperature from -40F to 250F. These carriers are used in applications such as robotics, pick and place, automation, mobile equipment, and machine tool. Nylon side-bands and metal crossbars can also be combined.
Metal Hose and Cable Carriers
Metal carriers or drag chains are very durable and work well with high operating temperatures. They also work well for heavy-duty workloads. Metal carriers are also superior for long, unsupported spans. They can also work at fast speeds or accelerations. They have good strength to weight numbers. Stainless steel carriers operating temperatures can go from -40F to 617F.
Choosing The Correct Cable or Hose Carrier
Some of the most important factors to consider in choosing carriers are the length of travel, how many cables or hoses will be in the carrier, the weight and the size of the hoses or cables, what speed of operation is needed, what acceleration there will be, and environmental factors involved. These factors can include harmful debris, intense heat, or chemicals.
These factors are important because, if a person gets it wrong, the carrier can fail in ways like snapping in half. Then, there is the choice between open and closed carriers that also depends on operating and environmental conditions.
The carriers will also have predetermined or multiple bending radii that must fit the cables or hoses and the operation conditions. It is good to choose a larger bend radius than the minimum required since this may help extend the life of the hoses and cables.
Pay close attention to the manufacturer’s suggested bend radius or the accepted guidelines from the NFPA79 2007. Remember, the bigger the bend radius, the less stress the cables and hoses will be subjected to and the longer they can last.
The minimum bending radius may be affected by other factors, including the operating temperature range. Low temperatures can make cables and hoses stiffer and require a larger bend radius, while high temperatures can make cables and hoses more flexible. Consult the manufacturer of the hoses or cables and the manufacturer of the carriers to get the correct pairing.